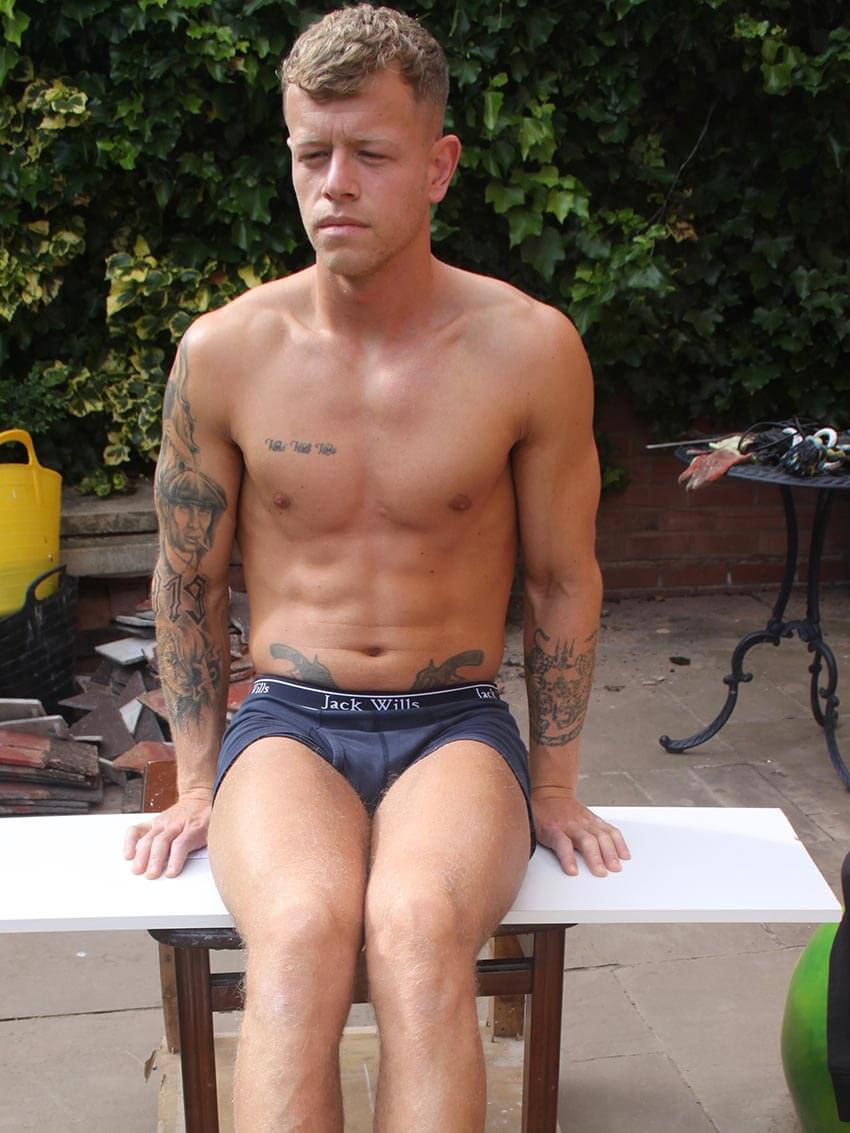
The Process
Design ideas
Phil and Fran begin their creative process by jointly exploring design ideas to make sculptures that will be engaging and enduring in a garden setting.
Whilst they are primarily inspired by the natural shapes of the human form and nature, their designs also consider the practicalities of casting and final display.
Once a design idea has been decided Fran then photographs a model to provide images for reference throughout the next stages of making the original artwork.
Sculpting
Initially Phil and Fran work together to design the armature for the original artwork to be built around. Phil makes these structures out of reclaimed wood and fixes them to moveable plinths, so they can be easily moved around during sculpting and the following processes.
The framework is a key feature in providing structure and stability for the modelling wax, which Fran then adds to the frame to create the sculpture.

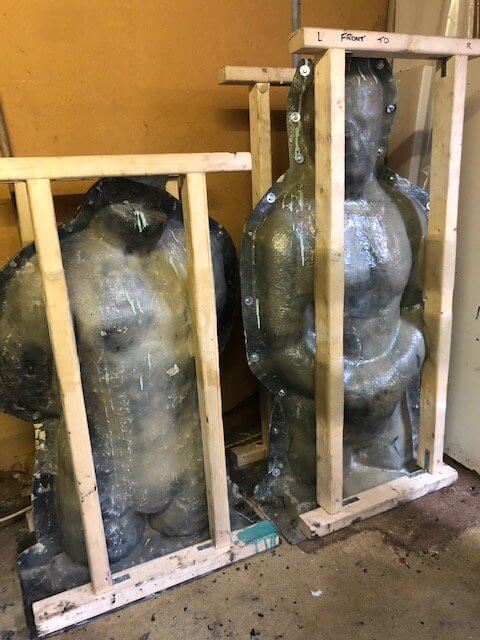
Mould
Once the original artwork is complete Phil covers it in a fine layer of silicone rubber which then forms part of the flexible rubber mould. This early addition in the process captures the artwork detail and protects it during the subsequent mould making stages.
Then Phil makes a fibreglass outer backing in order to provide support and structure to the silicone rubber mould. The fibreglass mould is made in sections so that it can be taken apart easily after casting to remove the casts of the sculptures.
This hard, outer mould also requires a frame to provide further structural support during the casting process.
Bronze cold casting
The mould is lined with a substantial quantity of bronze metal powder; this produces a finished cast that has the same feel and weathering properties of a traditional hot cast bronze.
The core of the mould is created by a cold pour that backs up the outer bronze wall, thus giving the sculpture strength and substance.
Refinement
Once the casting process is complete the cast is removed from its mould and positioned ready for its final, individual refinement.
Fran examines the sculpture and takes this opportunity to buff out any burrs and imperfections; and hand finishes the cast to an exacting standard reflecting the quality and finish of the original sculpture.
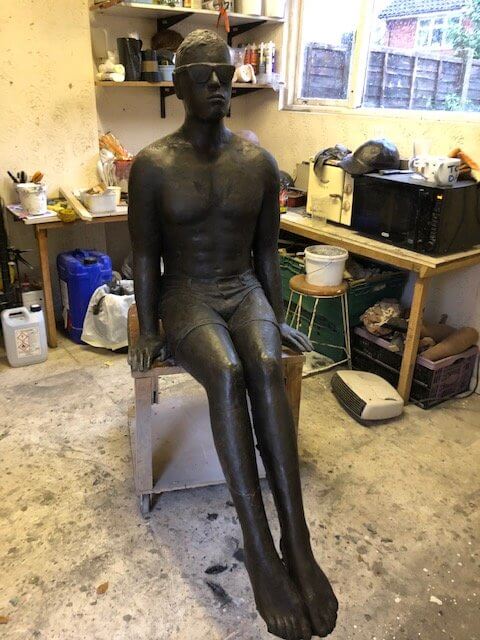
Frequently Asked Questions
What's the difference between cold cast & hot cast bronze?
The hot cast process is the traditional foundry way of producing a bronze, here molten metal is poured into a sand mould and left to cure. By contrast the cold cast method as the name suggests involves cold materials being poured into a mould that has been coated with a heavy layer of bronze powder.
How long will my sculpture last?
The sculpture is coated in bronze and cast with pretty much indestructible materials, bronze will oxidise when exposed to the elements developing the characteristic patina coating which is a sign of normal ageing, the sculpture it self will not deteriorate due to weather conditions.